About Us
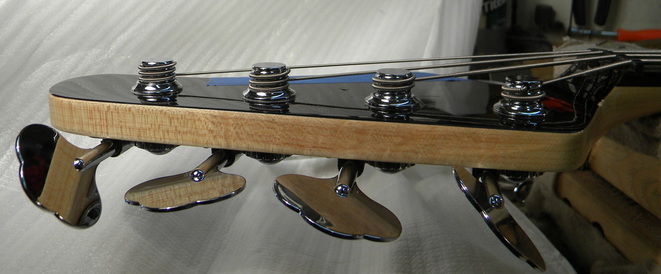
I have been custom building and repairing instruments for more than 30 years, not always just one at a time, I have factories that produce hundreds per day. Spending so much time and effort trying to make the products as good as possible mainly to stand the test of time.
However Basses always have problem’s with the truss rod, dead spots and many times fret buzz.
After spending what seemed like decades to figure out why the neck changes day by day depending on the humidity or when I travel with the basses, also many customers have brought their instruments in my shop mainly old P basses and J basses for adjustments. The truss rods are so tight that the bullet feels like it is going to snap and many times it does while trying to get the neck straight. This causes the action to be higher in the middle of the neck and it plays sharp when you press on the string (it is actually stretching it sharp).
The problem on basses is very simple, the truss rod stops at between the first fret and the nut, the headstock is 15mm thick (.590”) that is not strong enough for a straight paddle that is being pulled up from the strings and causing extreme stress on the neck.
Graphite necks, are great they don’t move but they are very expensive and you need to get a new bass or a new neck.
When electric basses were first designed manufactures used the machine heads that were available. They found that the D and G string did not stay in the nut because the string was directed to the middle of the machine heads post. The easiest solution was to screw a retainer on to hold the strings down. It was a quick FIX and the string goes down after the nut then back up toward the post. So the tip of the headstock is being pulled up causing unneeded tension on the neck, when a note is played it works like spring, Springs are absorbers and it absorbs the sustain until it stops.
So my idea was to stabilize the headstock from this spring action, trying many designs not wanting to modify the bass in any way. The best possible solution would be to have the strings come off the post at the lowest point possible. I did some testing and came up with a simple way of channeling the string to the lowest point on the machine head, stabilizing the headstock.
However Basses always have problem’s with the truss rod, dead spots and many times fret buzz.
After spending what seemed like decades to figure out why the neck changes day by day depending on the humidity or when I travel with the basses, also many customers have brought their instruments in my shop mainly old P basses and J basses for adjustments. The truss rods are so tight that the bullet feels like it is going to snap and many times it does while trying to get the neck straight. This causes the action to be higher in the middle of the neck and it plays sharp when you press on the string (it is actually stretching it sharp).
The problem on basses is very simple, the truss rod stops at between the first fret and the nut, the headstock is 15mm thick (.590”) that is not strong enough for a straight paddle that is being pulled up from the strings and causing extreme stress on the neck.
Graphite necks, are great they don’t move but they are very expensive and you need to get a new bass or a new neck.
When electric basses were first designed manufactures used the machine heads that were available. They found that the D and G string did not stay in the nut because the string was directed to the middle of the machine heads post. The easiest solution was to screw a retainer on to hold the strings down. It was a quick FIX and the string goes down after the nut then back up toward the post. So the tip of the headstock is being pulled up causing unneeded tension on the neck, when a note is played it works like spring, Springs are absorbers and it absorbs the sustain until it stops.
So my idea was to stabilize the headstock from this spring action, trying many designs not wanting to modify the bass in any way. The best possible solution would be to have the strings come off the post at the lowest point possible. I did some testing and came up with a simple way of channeling the string to the lowest point on the machine head, stabilizing the headstock.
Headstock Flex
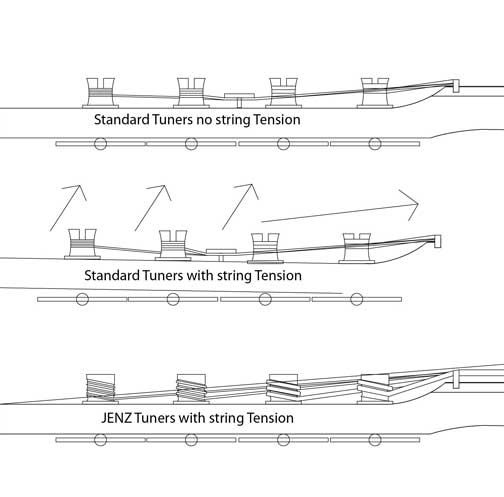
In the photo you can see how the string goes under the retainer then is direct back up towards the tuner, or pulling up on the headstock. The illustration below explains it.
The JENZ Tuners were designed to channel the string to any point on the machine head and eliminate the headstock from pulling up when tuned. You can see in the illustration below how the string tension is directed to the nut then the bridge.
Allowing very little headstock bow.
To better Illustrate we tested various basses with a dial caliper, the photo on the left are standard machine heads with no string tension and the caliper set to 0. The photo on the right is the same bass after being tuned to pitch, the small dial turned 3 times (300,000) and then 75,000, (375,000”)
Headstock Vibration
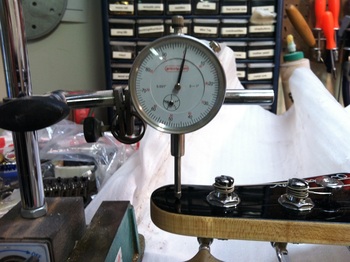
On a bass with JENZ machine heads we ran the same test. The photo on the left is a JENZ tuner set with no string tension set to 0. On the right, the same bass under string tension. The small dial did not go around and the large dial moved 50,000”, Almost nothing.
Straight Edge Test
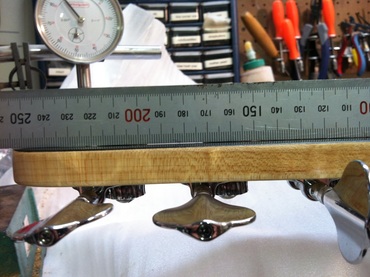
Another test using a straight edge. The photo uses old style machine heads with string tension. The light visible under the straight edge shows a bow in the headstock using the standard machine head design.
JENZ EQUIPPED

Same test on the JENZ Machine heads. The bass tuned to pitch, there is no bowing on the JENZ equipped headstock.